Our team of researchers is specialized in handling a wide range of gases, including dangerous ones. They are also experts in the associated separation processes. Through their three areas of expertise (absorption, adsorption, membranes), they measure the physical and chemical properties essential to characterizing systems involving gases, liquids, solids and membranes, using specific tools that operate under a broad spectrum of conditions. They develop and operate these systems on process pilots representative of real applications. The data collected are used to model and assess the technical and economic efficiency of the processes envisaged. Our expertise is applied to a wide range of topics including acid gas treatment and synthesis gases, the purification of biogases and hydrogen, CO₂ capture, gas dehydration, reducing the carbon footprint across the gas chain, and gas separation in petrochemical processes.
Experimental resources
From the laboratory to large-scale research facilities
For each sector, the laboratory is fitted with a set of tools ranging from thermodynamic, kinetic and structural data acquisition to the evaluation of the efficiency of technologies in conditions representative of the actual application conditions: gas solubility in solvents, absorption kinetics, gas adsorption capacity in porous solids, structural properties of adsorbents, adsorption kinetics, selectivity, membrane aging, solvent analyses, gas analyses, gas detection, etc.
CO₂ capture under test
Handling toxic, flammable fluids is the hallmark of this historic hub of expertise initially set up to pursue R&D on the sour gas extracted from the Lacq gas field in the 1960s. It has the skills, equipment and infrastructure needed to use these products in complete safety.
The handling of substantial quantities of H₂S (several dozen kg) as part of its research activities on acid gas separation is obviously one of its most noteworthy areas of expertise. However, its capabilities also include the handling of many other types of flammable and/or toxic gases – hydrocarbons, carbon monoxide, mercaptans, hydrogen – and synthesis gases (propylene and ethylene), which are used in research work to optimize processes for gas separation and treatment, and of course for CO₂ capture and transportation.
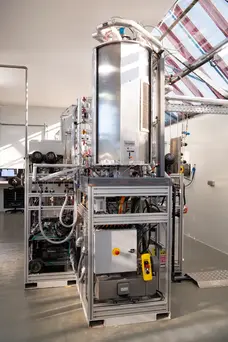
CO₂ capture demonstration unit
Pilot Platform, focused on new technologies
Since 2015, the six-hectare PPL site has been playing a crucial role for R&D in the SEVESO 3 plant at Lacq. Its purpose is to support the Company’s business and innovation activities by making it easier to set up large-scale experimental facilities and supporting their operation. The site is a testing area for new technologies in an industrial context, bridging the gap between laboratory tests and the deployment on site of innovative solutions, and is designed to receive pilots of all sizes to evaluate new processes or architectures.
TADI, a test site with international reach
The TADI (TotalEnergies Anomaly Detection Initiatives) site, at the PERL on the PPL, is a world-renowned facility used to test and qualify innovative gas leak detection and greenhouse-gas emission quantification technologies.
It is a vital facility, prior to site deployment, for gas detection and the quantification of atmospheric emissions. It is also home to an entire robotics ecosystem for the development of remote operations.
TADI was progressively constructed as from 2015, at the heart of a SEVESO 3 industrial site, which is almost the only one of its kind in Europe. It serves to test, perfect and qualify gas leak detection technologies, to ensure the safety of personnel and facilities, and has gradually been adapted to measure greenhouse gas emissions such as CO₂ and methane. Today, TADI is also a robot test site for remote operations systems. TADI was built using equipment from the former gas production plant (TEPF) – pipes, valves, tanks, columns, wellheads, flares – making it a realistic and modular industrial theater. A wide variety of gas leaks from on-site feedback can be reproduced in a controlled environment on TADI.
Over 400 tests on average are run each year on TADI. The site is acclaimed as a world reference test center. Fully backed by the European Commission and the United States Department of Energy, its international renown was further strengthened in April 2023, following the signature of a partnership with Colorado State University and its METEC program in the United States. The purpose of the partnership is to improve and standardize international protocols for testing gas emission detection and quantification technologies, to obtain reliable data that can be compared on an international scale.
- Read the article: Patrick Pouyanné meets the teams in the Béarn